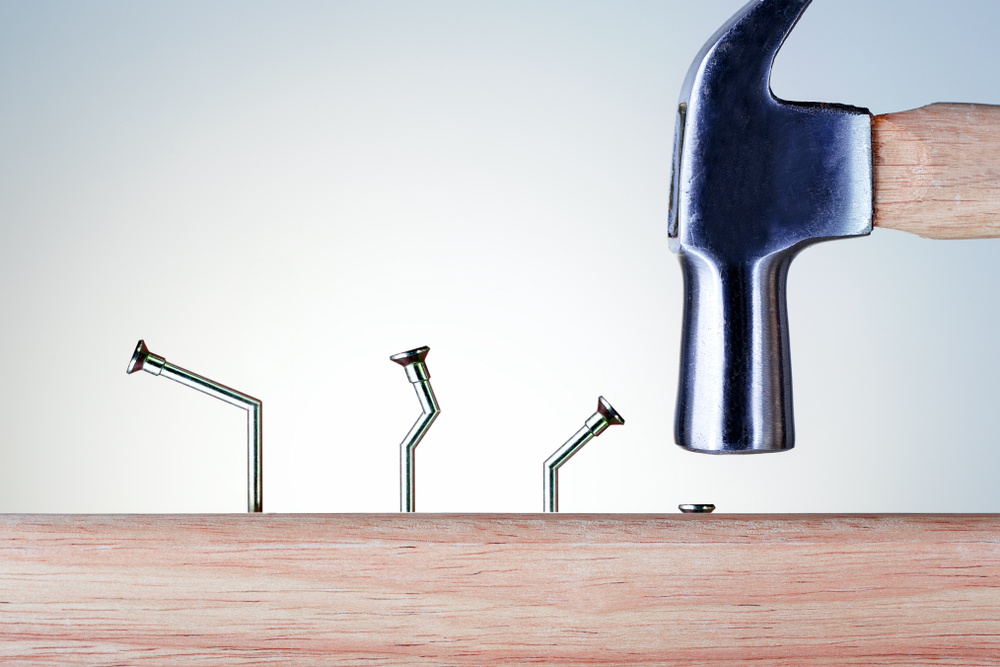
ポカミス防止の3ステップ!要因とポイント、ソリューション事例3社
製造現場や物流倉庫などの現場にとって、ポカミスは大きな問題です。ポカミスはすぐに解決できるものもありますが、そのまま原因を放置したまま対策せずにいると、いずれ経営に取り返しがつかなくなります。
当記事ではポカミス防止のために必要な考え方や検証について、さらにシステム的にポカミスを防止するソリューションを解説します。
もし、ポカミス防止のコンサルティングを受けて、
- 省力化、省人化してコストダウンしたい
- 生産性アップして売上を上げたい
- 人的ミスを減らして品質価値を高めたい
- どのメーカーの自動化設備を使えば効率的かわからない
という場合は、お気軽にFAプロダクツまでお問い合わせください。
関東最大級のロボットSIerとして、最適化のご提案をさせていただきます。
目次
1.ポカミスとは?ポカミスを防止するためのポイントを解説
(1)ポカミスとは?
製造現場や物流倉庫におけるポカミスとは、人為的なミスが原因で起こる現場でのさまざまなトラブルのことです。
現場によっては、人為的ミスそのものをポカミスと称することがあります。
また作業環境や使用工具、品質基準などの環境的な問題によって、ポカミスが誘発されるケースもよく見られます。
現場で発生するポカミスの例は次のとおりです。
- 作業中のよそ見が原因で、製品に異物が混入したり不良品を流した
- 検査のチェックミスで、製品回収や検品作業を行う事態に発展した
- 伝票や作業指示書の記入間違いで、発注や受注、出荷関係のミスが発生した
- 治工具や刃具のセットや使い方のミスによって、従業員がけがをした
(これは教育不足によるヒューマンエラーとも言えます)
- メンテナンス後のネジ締めや部品取り付け忘れなどで、機械の故障や製品不良などが発生した
- 在庫管理の数値打ち間違いにより、目視での数とデータ上の数が合わず、修正によって出荷が遅れる事態が発生した
以上の状況から見てもわかるように、ポカミスはほんの些細な油断や環境の問題から深刻な問題までさまざまな原因があります。
しかし引き起こされるトラブルが原因で会社の信用失墜や従業員の障害・死亡につながる可能性を考えると、原因に関係なくポカミスは防止する必要があります。
(2)ポカミスを防止するためのポイント
図1は、作業開始前のミーティングから、作業開始後にヒューマンエラーが発生し、調査とポカミス防止対策を検討するという流れのサンプルです。
ヒューマンエラーが発生したら、その要因を突き止めるための調査・打ち合わせを行うことが非常に重要です。
調査・打ち合わせによって、いろいろな職場の問題が浮き彫りとなります。
しかし、ポカミスを「うっかり」という言葉で簡単に片づけているケースも少なくありません。
「『うっかり』だからこれからは注意してやろう」などでその場を終わらせてしまいます。
それでは「うっかりミス」は今後とも続くでしょう。
なぜなら、ポカミスでも人が起こしたエラーで、ヒューマンエラーだからです。
「うっかり」は何らかの1次、2次の原因・要因があって発生します。
ヒューマンエラーが起こる背景は「うっかり」ではなく必ず、何らかの要因があります。
その要因を突き止めて、対策を講じることが大切なのです。
部品が散在する、書類が見つけにくい、仕事のルールがやりにくいなど不満に近いものが出てくるかもしれませんが、要因を突き止めるための調査・打ち合わせの狙いは、そこにあります。
ポカミスが起きるたびにこのような会議を重ねれば、職場の根本的な改善点が見えてきます。
それらを対策することで、ヒューマンエラーは限りなくゼロに近づけることができます。
注意点は、このような調査・打合せでミスを起こした人を責めないことです。全員が当事者という気持ちで臨むことが大切です。
また、対策を突き詰める中で、「この作業は人がやると必ずエラーが起こるのだから、自動化の設備で対応すべき」という意見が出ることもあるかもしれません。そのようなときは、なぜ設備がないとエラーが起きるのかという、人に対する原因・要因を明確にすることが大切で、設備がないことを安易に原因としないようにしましょう。
2.ポカミスを防止するための3ステップ
ポカミス防止ステップ1:要因を把握する
ポカミスを防止する最初のステップは、「なぜミスが発生するのか」「どこでミスが発生しているのか」など、ポカミス発生の要因を把握することです。ポカミスの原因がわからなければ、防止策も取りようがありません。
現場の分析や従業員へのヒアリング、全体のモニタリングなどを行い、ポカミスの原因を追求し、問題の顕在化を進めることから始めます。
客観的に見るとポカミスとすぐに分かる場合でも、作業をしている従業員の認識や行動によって、ポカミスが潜在化しているケースがあります。経営者や管理者、安全担当者、経験・スキルが異なる作業者など実際に作業してみて、それぞれが感じた問題点をまとめるのも効果的です。
ポカミスの多くはヒューマンエラーです。しかし「ただのヒューマンエラーだから次から気をつけらばよい」と詳細な要因まで追求せずに放置すれば、同じ作業者および他の作業者が同じミスを繰り返す可能性があります。
以下では、ポカミスの要因としてよく挙げられるものをピックアップしました。
ポカミスの要因①ルールの不備・形骸化
製造現場には、製造を行う上での作業マニュアル(作業標準書)や品質検査基準、安全関係の手順書などのルールが設定されています。しかし、これらのルール自体の不備が原因で、ポカミスが発生する可能性があります。
例えばNGの基準やルールを守る目的、具体的な指示内容が曖昧になっているケースです。ルール解釈が作業員任せだと、多様なポカミスが発生する可能性が高くなります。
作業員の判断で「守らなくても大丈夫だろう」と、ルールが形骸化している場合もあるでしょう。このような「暗黙のルール」の存在は、将来的なクリティカルポイントになるリスクがあります。
しっかり遵守した場合でも、そもそもがトラブル防止効果が薄い内容だったなど、ルールに問題があるケースも考えられます。
ポカミスの要因②作業員の能力・訓練不足
もし危険箇所や作業の注意点が共有化され、適切なルールが定まっていたとしても、作業員のスキルや精神状態、疲労加減、緊張加減などの個人の問題がポカミスの原因になる可能性があります。また、新入社員や中途採用者が作業に当たる場合、ルールの確認不足や機械操作の訓練不足などが要因でポカミスとなる場合も少なくありません。
ポカミスの要因③ヒューマンエラーが起きやすい作業環境
ルールや作業員に問題がなくても、作業環境自体がポカミスを誘発するケースも考えられます。例えば、次のような作業環境です。
- 治工具や部品が散乱していて作業者が混乱する状況である
- 作業スペースが狭く、機械や他作業者との接触が頻繁に発生する
- 1つの工程で複数人が関わり、作業がクロスする状態である
- 作業場の温度調整が難しく、暑い夏や寒い冬にて作業員の疲労が溜まりやすい状況である
- 治工具や機械・設備、操作ボタンなどにラベリングやその他表示されておらず、作業者の誤解を招く
ポカミス防止ステップ2:ポカミス防止策を検討する
要因把握が終了した後は、具体的な防止策を検討しましょう。例えば前見出し「ポカミスを誘発する作業環境」の例だと、以下の防止策が考えられます。
- 治工具・部品置き場の決定・遵守、置き場の新設、定期的な5Sの実施
- 作業員の作業動線や機械・設備の設置位置の変更
- 作業分担の明確化、お互いの進捗状況を記載するノートやホワイトボードを設置、作業中の声掛けの徹底
- スポットクーラーやその他空調システムの設置、ウィータークーラーの設置
- ラベリングの実施(ラベリング剥がれなどによる異物混入に注意)
防止策において大切なことは、「同じ作業者が同じミスをしないこと」「スキル・経験に関わらず、誰が作業してもポカミスの防止につながること(フールプルーフ設計)」「一時しのぎよりも、根本的な問題を取り除く対策の立案を優先すること」などが挙げられます。
作業のルール化とともに、必要に応じて従業員の教育や訓練も実施してください。過去のポカミス事例や対処法をまとめたり、現場の危険箇所・発生したミスなどを記載するノートを用意したりの対策もおすすめです。
また、防止策の策定で注意したいのは、手段が目的になるケースです。例えば作業のダブルチェック実施や点検項目の増加は効果を見込めますが、チェック作業や点検箇所が増え過ぎるとかえって見逃しが発生しやすくなり、新たなポカミスの発生につながります。
「なぜルールを守る必要があるのか」を徹底的に周知し、作業員が進んで遵守するものが理想です。
ポカミス防止ステップ3:実施した防止策の効果検証を行う
ポカミス防止策を実施した後は、防止策が本当に効果があったのかを検証します。
まず検証に関して大切なことは、「防止策を実行する前の状態」を事前に分析・記録しておくことです。
実行前後での比較ができなければ、本当に効果があったのかは作業員の肌感覚や予想でしか判断できません。分析結果や防止策を将来的なナレッジとする意味でも、ヒアリングやモニタリングの結果を記録し、資料として残しておきましょう。新入社員の教育や新設備導入など、ポカミスが発生しやすい状況になったときにも、その資料は役に立つはずです。
効果検証を行う際は、実行前のデータと比較しながら進めます。検証方法は製造現場の状況や実行した防止策によって異なるので、現場に応じた検証方法を実行してください。効果検証でのチェックポイントとして、例えば次のものが考えられます。
- 時間に対する作業員の不注意・ミスの数を測定し、実行前後で比較する
- 作業員の作業感や疲労度、チェックのやりやすさなどをヒアリングする
- 防止策を実行した箇所での作業をスキル・能力が異なる複数人に行わせ、標準化がなされているか一定期間測定を続ける
- 防止策の実行によって新しい問題が発生しないか確認する
もし検証した結果が芳しくなかった場合は、「なぜ効果がなかったのか」「防止策の改善点は何か」など、防止策の実行前と同じように要因把握・防止策の検討・実行のステップを踏んでください。
【関連動画】
【ヒューマンエラー防止方法】すぐに出来る作業員の対策
引用:https://www.youtube.com/watch?v=Bv7lVcc5Lwo
ヒューマンエラー未然防止3つのしくみ
引用:https://www.youtube.com/watch?v=qj5OYCRbWs8
ポカヨケを4ステップで設計・導入しましょう(ポカミス防止)【トヨタ生産方式】
引用:https://www.youtube.com/watch?v=EcFBnOhhIiw
3.ポカミスを防止するのに役に立つソリューションを提供する会社3選
ヒューマンエラーの特性上、どれだけ詳細なルールや作業しやすい環境を整えても、ポカミスを完全にゼロにするのは困難です。ポカミスをゼロに近づけるには、機械的に制御・検査する仕組みの導入も積極的に検討しましょう。
以下ではポカミスを防止するのに役に立つソリューションを提供する、おすすめの会社を3つご紹介します。
(1)株式会社FAプロダクツ
日本サポートセンターは、年間200台のロボット導入実績や画像処理技術のノウハウなどを持つ、関東最大級のロボットSIerです。2021年より沖電気工業株式会社の組立作業者支援ソリューションである「プロジェクションアッセンブリーシステム」に関するシステムパートナーとなりました。
【ソリューション紹介】
引用:https://www.youtube.com/watch?v=2IYRrVRftF0
「プロジェクションアッセンブリーシステム」とは、プロジェクターによる作業ナビゲーションと高度なセンシングを活用した作業履歴のデジタル化、作業結界のデジタルデータ化などを実現する組立作業ナビゲーションです。工程に応じて部品を取る場所を誘導することで、作業ミスの減少と効率向上を実現します。また各種データ化により、問題点の抽出ができ、実績の蓄積にも寄与します。
【所在地】
〒300-0847 茨城県土浦市卸町2-13-3
TEL.050-1743-0310(代表)
FAX.050-3156-2692(代表)
https://jss1.jp/
(2)株式会社キーエンス
株式会社キーエンスは、新しく製造する製品の約7割が「世界初」や「業界初」である、日本を代表するメーカです。センサや制御機器、画像処理関係、精密機器など、さまざまな事業を展開しています。
【ソリューション紹介】
株式会社キーエンスでは、さまざまな業界・現場に対応できるポカミス防止ソリューションを提供しています。例えば次のとおりです。
- ハンディターミナル:バーコード読み取り間違いを防止し、在庫管理やコンベアラインの検査でのポカミスを減らす
- 画像処理システム(XG-XやCV-Xシリーズなど):異物混入や印字状態、表面のキズ、光沢などをチェック・検出する
- センサー各種(光電センサやファイバセンサなど):可視光線や赤外線や近接など、状況に応じたさまざまな検出を行うセンサー
上記のように、人間の目では見逃したり見間違えたりするところのチェックを実施できるものが揃っています。
【所在地】
〒533-8555 大阪市東淀川区東中島1-3-14
TEL.06-6379-1111
FAX.06-6379-2222
https://www.keyence.co.jp/
(3)エレコムグループ
エレコムグループは、業務効率化や生産性向上、BCP対策、セキュリティなど、あらゆる現場の課題を解決するソリューションを展開するメーカです。
【ソリューション紹介】
エレコムグループでは、製造現場や物流倉庫で使えるさまざまなポカミス防止ソリューションを提供しています。例えば次のとおりです。
- ネットワークカメラ(VIVOTEK製品):逆光下や暗闇対応、人物検知、180°パノラマカメラなど、現場の必要に応じた監視用カメラ
- ZEROSHOCKタブレット:装置や設備の点検業務や報告書作成を効率化させ、点検抜けや記入漏れを防げるタブレット端末
詳細な製品情報は、各グループ企業にお問い合わせください。
【所在地(エレコム株式会社)】
大阪市中央区伏見町4丁目1番1号明治安田生命大阪御堂筋ビル9F
TEL:0570-067-676
FAX:0570-005-900
https://www.elecom.co.jp/
https://solution.elecom.co.jp/
4.ポカミス防止ソリューションならFAプロダクツにお任せください
人間が作業する限り、製造現場におけるポカミスは必ず発生します。しかし、ポカミスの被害を小さくしたり、ポカミスの発生をゼロに近づけたりすることは、製造現場において非常に重要です。
ポカミスを防止するためには、要因把握によって問題点を抽出し、適切な防止策を策定します。また、ポカミス防止につながるシステム的なソリューションを組み合わせることで、より防止効果を高められるでしょう。
もしFAプロダクツがシステムパートナーを務める沖電気株式会社の「プロジェクションアッセンブリーシステム」についてご相談がありましたら、ぜひ弊社へお問い合わせください。プロジェクションアッセンブリーシステムの取扱のほか、連係するシステムや作業、工程の自動化などについて、一貫して対応いたします。
【特徴】
FAプロダクツは年間200台もの実績がある関東最大級のロボットシステムインテグレーターです。一貫生産体制をとっており、設計から製造までをワンストップで対応。費用・時間にムダなく最適化を行うことができます。
また、お打ち合わせから原則1週間以内に「お見積りとポンチ絵」をご送付。
【ポンチ絵とお見積りのサンプル】
テキストやお電話だけでは伝わりづらいゴールイメージを共有し、スピード感を持った対応を心がけています。
また、同社の「画処ラボ」では、画像処理を用いた外観検査装置の導入に特化し、ご相談を受け付けています。従来は目視での官能検査に頼らざるを得なかった工程の自動化をご検討の際などにご活用ください。
業界最大級の画像処理検証施設を開設!
「画処ラボ」ではルールベースやAIの画像処理を専門エンジニアが検証。ご相談から装置制作まで一貫対応します。
【所在地】
茨城県土浦市卸町2丁目13-3
TEL.050-1743-0310(代表)
FAX.050-3156-2692(代表)
https://jss1.jp/
【営業品目】
- 産業用ロボット
- 生産設備合理化・省力化の設計及び製作
- 基板電気チェッカーや貼合・折曲など
- 治具の設計・製作
【実績】
NM社(電子部品の製造販売)、HS製作所(情報通信・社会産業・電子装置・建設機械・高機能材料・生活の各システム製造販売)、TT社(ショッピングセンターなどリテール事業)、SM社(自動制御機器の製造・販売)、OR社(自動車安全システムの製造販売)