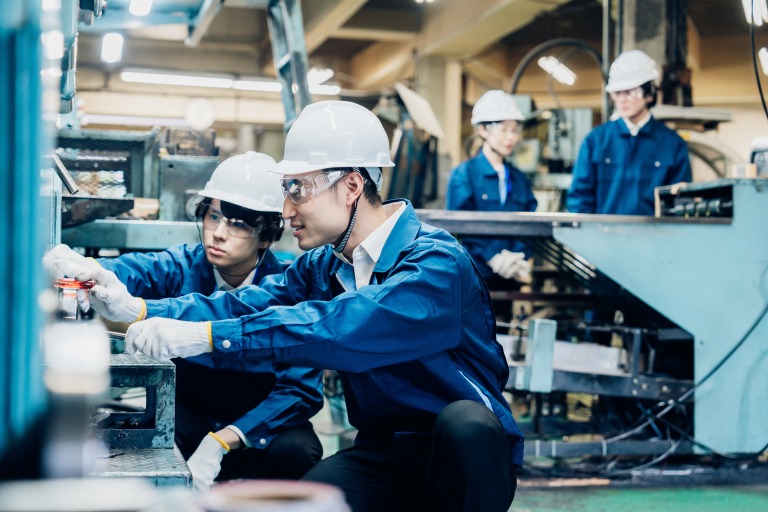
ガンドリル加工とは?特徴や仕組み、加工条件、BTA加工との違い
ガンドリル加工は、高精度な深穴加工を可能にする技術で、自動車、航空宇宙や医療機器など、精密な部品が求められる分野では欠かせない加工方法です。
本記事では、ガンドリル加工の基本技術、BTA加工との違い、性能や特性の比較、そして最新の技術動向について詳しく解説します。
ガンドリル加工のコンサルティングを受けて、
・省力化、省人化してコストダウンしたい
・生産性アップして売上を上げたい
・人的ミスを減らして品質価値を高めたい
・どのメーカーの自動化設備を使えば効率的かわからない
という場合は、お気軽に株式会社FAプロダクツまでお問い合わせください。
関東最大級のロボットSIerとして、最適化のご提案をさせていただきます。
目次
1.ガンドリル加工とは?その特徴
ガンドリル加工は、深穴加工に特化した技術として、さまざまな産業で不可欠な存在です。
ここでは、ガンドリル加工について、概要と特徴を解説します。
(1)ガンドリル加工とは
ガンドリル加工は、高精度な深穴加工を行うことができる技術です。
深穴加工とは、穴の深さが直径の10倍以上となる穴あけ加工です。通常のドリルでは工具の剛性不足や切り屑の排出問題により深穴を高精度で加工することは難しい一方で、ガンドリル加工は、切削時に刃先を冷却し摩耗を抑えながら切り屑を排出するための冷却液(クーラント)を工具内部に循環させながら切り屑を効率的に排出する仕組みを備えており、加工精度と安定性の両立が可能です。
また、ガンドリルの特徴として「L/D比(長さ/直径比)※」が大きく、通常の加工では精度が維持ができないような深穴でも、直進性を確保しながら加工することが可能です。
たとえば、直径5mmで100mm以上の穴を高精度に加工できるため、極細部品にも対応します。
※L/D比:穴の深さ(L)を穴径(D)で割った値。たとえば穴の深さが100mmで直径が10mmの場合、L/D比は10となる。L/D比が大きくなるほど加工が難しくなり、適切な工具や加工条件が求められる。
(2)ガンドリル加工の特徴
ガンドリル加工の特徴は以下の通りです。
① L/D比が大きい穴の加工が可能
通常のドリルでは、直径の10倍以上の深さの穴を開けると、ドリルのたわみや切り屑の詰まりが発生しやすくなります。
ガンドリルなら、加工穴の中心軸からドリルがズレないように固定する専用のガイドブッシュとクーラント供給システムを活用し、L/D比50以上の深穴でも高精度に加工できます。
② 小径穴の直進性を確保
直進性とは、穴あけ加工における直線性を指します。
小径の穴では、わずかな工具のブレが穴の品質に大きく影響します。
ガンドリル加工では、ガイドブッシュによりドリルのブレを最小限におさえながら加工を行い、高精度な穴あけと優れた直進性を実現します。
③ 表面粗さの向上
表面粗さとは、加工後の穴の内面の滑らかさを示す指標です。
ガンドリル加工では、刃先の特殊な形状によって加工面が滑らかになり、追加の仕上げ加工が不要な場合もあります。
また、切削中にクーラントを内部から供給し、摩擦を低減することで、加工面の品質を向上させることができます。
④ 切り屑の効率的な排出
深穴加工では、切り屑が内部に残ると加工不良の原因になります。
ガンドリルは内部クーラント供給方式を採用し、切り屑を効率よく排出することで、穴の精度を維持します。
【参考動画】ガンドリル加工については以下の動画も参考にしてください。
引用:DeepTri-Drilll【ディープ・トライ・ドリル】 – 安定した高能率加工と刃先交換式による管理の容易性
2.ガンドリルの構造と仕組み、用いられる素材
ここでは、ガンドリルの構造や仕組み、素材、加工条件について解説します。
(1)ガンドリルの構造と仕組み
ガンドリルは、深穴加工を高精度で行うために設計された特殊な工具で、主に小径で高精度な穴あけに使用されます。
ガンドリルの構造は、以下の3つの要素から成り立っています。
・刃先 ・シャンク部 ・クーラント流路 |
以下で詳しく解説します。
① 刃先(切削部)
役割 | 穴を削り、精度を確保 |
ガンドリルの刃先は、1枚刃または2枚刃で構成され、ワークの材質や加工条件に応じた最適な角度で設計されています。刃先角度の適正化により、工具のブレを最小限におさえ、切削抵抗を減らすことで、安定した加工が可能です。
また、使用されるチップにはブレーカー機能がそなわっており、長くなりがちな切り屑を細かく砕いてスムーズに排出します。適切なチップブレーカーを選定することで、切削抵抗を最小限におさえながら、加工精度を向上させることが可能です。
② シャンク部
役割 | 工具の剛性を維持 |
シャンク部は、加工中の剛性を確保するための重要なパーツです。
とくにL/D比(長さ/直径比)が大きい深穴加工では、工具のたわみを最小限におさえるために、高剛性の材料が用いられます。
また、シャンク部分には、クーラント供給のためのクーラントホールが配置されており、切削時の熱を効率よく冷却します。
③ クーラント流路
役割 | 冷却と切り屑排出 |
ガンドリルの最大の特徴は、工具内部にクーラントが流れる穴(クーラントホール)が組み込まれていることです。
クーラントは高圧で供給され、切削部で発生する摩擦熱を冷却しながら切り屑を流し出します。
「クーラントスルー(Coolant Through)」や「インターナルクーラント(Internal Coolant)」と呼ばれる冷却機構により、長時間の連続加工でも高精度を維持できます。
(2)ガンドリル加工で用いられる素材と適用例
ガンドリル加工では、以下の素材が主に使用されます。
素材 | 特徴 | ガンドリル加工の適用例 |
炭素鋼・合金鋼 | 強度が高く、耐摩耗性に優れる | 自動車部品、航空機部品 |
ステンレス鋼 | 耐食性が高く、硬度が高い | 医療機器、食品加工機械 |
アルミニウム | 軽量で熱伝導性が良い | 精密機械、航空宇宙産業 |
銅・銅合金 | 電気・熱伝導性が高い | 冷却システム、電子機器 |
チタン | 高強度・軽量・耐熱性に優れる | 航空宇宙、医療機器 |
インコネル・ハステロイ | 高温・高圧環境に耐える | 航空エンジン、化学プラント |
3.ガンドリル加工の種類とメリット・デメリット
ガンドリル加工は、加工対象や設備環境に応じて、いくつかの方式に分類されます。
主な分類として、専用機を用いる方法とマシニングセンタ用アタッチメントを活用する方法の2つがあります。
それぞれ加工精度、作業効率、コストに違いがあり、用途に応じた最適な方法を選択することが重要です。
(1)ガンドリル専用機による加工
ガンドリル専用機は、深穴加工を高精度かつ安定的に行うために設計された設備です。
通常、L/D比(長さ/直径比)が50以上の穴でも直進性を維持しながら高精度な加工が可能です。
専用機には以下のようなメリット・デメリットがあります。
メリット | ・高精度な直進性を確保しやすい。 ・高圧クーラントシステムを備え、切り屑の排出効率が高い。 ・高速加工が可能で、大量生産向き。 |
デメリット | ・初期投資が高く、専用機が必要。 ・設置スペースを取るため、小規模な工場には不向き。 ・小ロット生産にはオーバースペックになる可能性がある。 |
(2) マシニングセンタ用アタッチメントによるガンドリル加工
マシニングセンタ用アタッチメントを活用したガンドリル加工は、汎用性の高いマシニングセンタを使って深穴加工を行う方法です。
専用機ほどの高精度・高速加工は難しいですが、既存の設備を活用できるため、コストを抑えながら導入が可能です。
マシニングセンタ用アタッチメントを活用したガンドリル加工には、以下のようなメリット・デメリットがあります。
メリット | ・既存のCNCマシニングセンタに取り付けるだけで導入可能。 ・深穴加工以外の加工にも対応できる。 ・小ロットや試作品の加工に向いている。 |
デメリット | ・高精度な深穴加工には制約がある(L/D比が大きい加工には向かない)。 ・クーラント供給や切り屑排出の効率が専用機ほど高くない。 ・専用機と比べると加工速度が遅い。 |
4.ガンドリル加工のプロセスと加工条件
加工工程は、工具の準備、ワークの固定、回転と送り動作、切り屑の排出、仕上げの確認という流れで進行し、各ステップで精密な制御が求められます。
とくに切削中の冷却と切り屑の排出が加工精度を大きく左右します。
ここではガンドリル加工のプロセスと加工条件を説明します。
(1)ガンドリル加工のプロセス
ガンドリル加工のプロセスは以下の通りです。
①工具の準備 ・加工する材料に応じた適切なガンドリルを選定する。 ・刃先の摩耗状態を確認し、必要であれば新品のチップに交換する。 ・クーラント供給経路をチェックし、十分な圧力がかかるよう調整する。 |
▼
②ワークの固定 ・治具(ジグ)を使用し、ワークを正確な位置に固定することで振動やズレを防ぐ。 ・ガイドブッシュを用いることで、ドリルのブレをおさえ、直進性を確保する。 |
▼
③回転と送り動作 ・適切な回転速度(rpm)と送り速度(mm/min)を設定し、材料の特性に応じた切削条件を選定する。 ・加工初期は低速で慎重にドリルを進め、安定した削り出しを行う。 |
▼
④切り屑の排出 ・高圧クーラントを供給し、刃先の冷却と同時に切り屑を排出する。 ・切り屑が排出経路に詰まると加工不良の原因になるため、適切な流量を維持する。 |
▼
⑤仕上げと精度確認 ・加工後、ボアゲージやエアマイクロメーター、さらには光学プローブやX線CTスキャナーを活用することで穴径や直進性を検査する。 ・必要に応じて追加の仕上げ加工を行い、最終的な寸法精度を確保する。 |
(2)ガンドリル加工の加工条件
ガンドリル加工では、アスペクト比(L/D比:穴の深さ(L)と直径(D)の比率)が大きくなるほど、以下のように加工の難易度が増し、直進性の確保が難しくなります。
工具のたわみ | 工具が長くなることで、加工中にたわみが発生し、穴の直進性が低下する可能性があります |
切り屑の排出不良 | 深い穴では、切り屑が効果的に排出されない場合があり、加工精度や工具寿命に悪影響を及ぼすことがあります |
熱の蓄積 | 深穴加工では、熱がこもりやすく、工具の摩耗や加工精度の低下を招くことがあります |
直進性を向上させるためには、以下のような対策が必要です。
適切な工具の選定 | 加工する材質やアスペクト比に応じて、最適なガンドリルを選択する |
ガイドブッシュの使用 | 加工開始時に工具の軌道を安定させるために、ガイドブッシュを使用することで、直進性の確保が容易になる |
クーラントの供給 | 高圧の切削油を供給することで、切り屑の排出を促進し、熱の蓄積を防ぐことができる |
適切なチップの選定 | 適切なチップを選定し、切り屑を細かく分断することで排出効率を高めることが可能 チップは加工する鋼材材質に適したコーティングを選ぶ |
加工条件の最適化 | 回転速度や送り速度を適切に設定することで、工具のたわみや振動を抑制し、直進性を向上させることが可能 |
また、回転速度や送り速度、クーラント圧力は、工具の直径や加工する素材によって大きく変動するため、素材に合わせた適切な条件設定も重要です。
たとえば、小径工具では高回転が適し、大径工具では低回転が推奨されます。硬度の高い素材ほど送り速度を低く設定し、クーラント圧力を適切に調整することが重要です。
最適な加工条件は、メーカーの推奨値や加工現場での実績を参考に決定する必要があります。
5.ガンドリル加工とBTA加工の違い
深穴加工には、ガンドリル加工とBTA加工の2つの主要な技術が存在します。
どちらも高精度な穴あけを実現するために使用されますが、加工方式や適用範囲、効率の面で異なる特性を持っています。
ここではガンドリル加工とBTA加工の違いを解説します。
(1)ガンドリル加工の特徴
ガンドリル加工は、小径(一般的に1mm~30mm)の深穴加工に適した技術です。
ガンドリル加工では、工具の内部を通してクーラント(切削油)を供給します。切り屑は工具外側の溝(フルート)を通じて排出されるため、排出時に切り屑が加工面に接します。
ガンドリル加工の特徴は以下の通りです。
精度と直進性 | ・優れた直進性と高精度な穴あけが可能 ・特にL/D比(長さ/直径比)が50以上の細長い穴の加工に適している |
滑らかな仕上げ面 | 加工後の穴の内面は滑らかで、追加の仕上げ加工が不要な場合が多い |
適用範囲 | 自動車部品(例:クランクシャフトのオイル供給穴)、航空宇宙部品、医療機器など、小径で高精度な深穴が求められる分野で広く使用されている |
加工効率 | ・小径の深穴加工では、ガンドリル加工は高い直進性と精度を維持しながら効率的に加工を行える ・一方、穴径が50mm以上になると加工時間の増加や工具の摩耗などにより効率が低下 |
(2)BTA加工の特徴
BTA(Boring and Trepanning Association)加工は、中径から大径(一般的に20mm以上)の深穴加工に適した技術です。
BTA加工では、クーラントを工具の外側から供給し、切り屑は工具内部を通じて排出します。切り屑が加工面に接することがありません。
BTA加工の特徴は以下の通りです。
高効率な切り屑排出 | 工具内部を通じて切り屑を排出するため、大量の切り屑を効率的に処理できる |
高速加工 | ガンドリル加工と比較して、加工速度が速く、生産性が高い |
適用範囲 | 大型エンジンブロックの冷却流路、油圧シリンダー、航空機のランディングギアなど、大径で深い穴が必要な部品の加工に適している |
加工効率 | ・大径の深穴加工では、BTA加工は切削速度が速く、大量生産やコスト効率が求められる場合に有利 ・とくに直径50mm以上の大径穴の加工では、ガンドリル加工よりも加工時間を大幅に短縮可能 |
6.ガンドリル加工が求められる分野と最新技術
ここでは、ガンドリル加工が活用されている分野と、最新技術について紹介します。
(1)ガンドリル加工が求められる分野
近年、製造業全体の高精度化と効率化の要求が高まり、ガンドリル加工の重要性が一層増しています。
とくに自動車、航空宇宙、医療機器などの分野では、製品の小型化・軽量化が進む中、以下のようなシーンでより精密で安定した深穴加工技術が求められています。
自動車業界 | エンジンのクランクシャフトや燃料噴射システム部品の精密な深穴加工 |
航空宇宙分野 | ジェットエンジンの冷却システムの深穴加工 |
医療分野 | 注射針や内視鏡のシャフト、人工関節の微細穴など、微細で精密な穴あけ加工 |
以下で詳しく解説します。
①自動車業界
自動車業界では、エンジン部品やEVバッテリーの冷却システムの流路加工において、L/D比50以上の高精度な深穴加工が求められています。
エンジンの燃料噴射システムでは、燃料の流量や噴射圧を均一にするために、精密な穴あけ加工が必要です。
また、EV(電気自動車)の冷却システムでは、バッテリーの温度管理を最適化するために、複雑な流体経路を精密に形成する技術が求められています。
②航空宇宙産業
航空宇宙産業では、ジェットエンジンの冷却穴や燃料供給経路の精密加工が不可欠です。
とくにエンジンの燃焼効率を向上させるために、熱負荷を適切に分散させる冷却システムが導入されており、L/D比100を超える超深穴加工が求められるケースも増えています。
航空機の軽量化と耐久性向上のため、チタンやインコネルなどの難削材の加工技術も発展しており、ガンドリル加工の適用範囲が広がっています。
③医療分野
医療分野では、カテーテルや人工関節の微細穴加工が不可欠です。
医療機器では、極めて細かい穴が必要とされることが多く、たとえば内視鏡や注射針には直径1mm未満の精密な穴が求められます。
従来の加工技術では、バリの発生や穴の歪みが課題となっていましたが、最新のガンドリル加工技術により、精密な仕上がりと安定した品質を確保することが可能になりました。
さらに、AIやIoT技術の導入によって、ガンドリル加工の精度向上と生産性の最適化が進んでいます。
最新のガンドリルマシンは、加工中の工具摩耗や切削状態をリアルタイムで監視し、AIが最適な加工条件を自動調整することで、より安定した品質を確保できます。
また、超高圧クーラント技術の進化により、切り屑排出性能が向上し、より長尺で直進性の高い穴加工が実現されています。
(2)ガンドリル加工の最新技術
ガンドリル加工は、新素材の開発やデジタル技術の進化に伴い適用範囲が拡大しています。
ここでは、ガンドリル加工の最新技術を紹介します。
① CNC技術の進化による加工精度向上
CNC制御の導入により、加工パラメータの最適化が可能になり、送り速度や回転速度を細かく調整することで、直進性や寸法精度の向上が実現されています。
また、加工中の振動や工具摩耗をリアルタイムで補正する機能が搭載され、より安定した深穴加工が可能となっています。
②高圧クーラントシステムの改良
切り屑の排出と工具の冷却は、ガンドリル加工において重要な要素です。
最新のガンドリルマシンでは、超高圧クーラント供給システムが導入され、より深い穴や難削材の加工でも安定した切り屑排出と工具寿命の延長が可能となっています。
③AIとIoTによるスマートガンドリルマシン
近年、AIやIoTを活用した加工監視システムが導入され、加工中のデータをリアルタイムで分析し、最適な加工条件を自動調整する技術が発展しています。
先端技術により、加工不良の発生を最小限におさえ、工具寿命の最適化と生産性の向上が実現されています。
④国際特許技術の開発
株式会社ハイタックは、独自の主軸スピンドルと国際特許を取得した機構により、最大L/D(長さ/直径比)400の深穴加工を実現しています。
従来の加工方法では難しかった極小径や超深穴の加工が可能となり、医療、航空宇宙、自動車など多様な分野での応用が期待されています。
7.ガンドリル加工に関するご相談は株式会社FAプロダクツへ
FAプロダクツは年間200台もの実績がある関東最大級のロボットシステムインテグレーターです。一貫生産体制をとっており、設計から製造までをワンストップで対応。費用・時間にムダなく最適化を行うことができます。
ガンドリル加工についても、ぜひご相談ください。
お打ち合わせから原則1週間以内に「お見積りとポンチ絵」をご送付いたします。
【ポンチ絵とお見積りのサンプル】
テキストやお電話だけでは伝わりづらいゴールイメージを共有し、スピード感を持った対応を心がけています。
また、同社の「画処ラボ」では、画像処理を用いた外観検査装置の導入に特化し、ご相談を受け付けています。従来は目視での官能検査に頼らざるを得なかった工程の自動化をご検討の際などにご活用ください。
業界最大級の画像処理検証施設を開設!
「画処ラボ」ではルールベースやAIの画像処理を専門エンジニアが検証。ご相談から装置制作まで一貫対応します。
所在地・連絡先等 | 営業品目 | 実績 |
茨城県土浦市卸町2丁目13-3 TEL.050-1743-0310(代表) FAX.050-3156-2692(代表) https://jss1.jp/ |
・産業用ロボット ・生産設備合理化・省力化の設計及び製作 ・基板電気チェッカーや貼合・折曲など ・治具の設計・製作 |
NM社(電子部品の製造販売)、HS製作所(情報通信・社会産業・電子装置・建設機械・高機能材料・生活の各システム製造販売)、TT社(ショッピングセンターなどリテール事業)、SM社(自動制御機器の製造・販売)、OR社(自動車安全システムの製造販売) |
関東最大級のロボットシステムインテグレーター 生産設備の設計から製造ならお任せください
050-1743-0310 営業時間:平日9:00-18:00