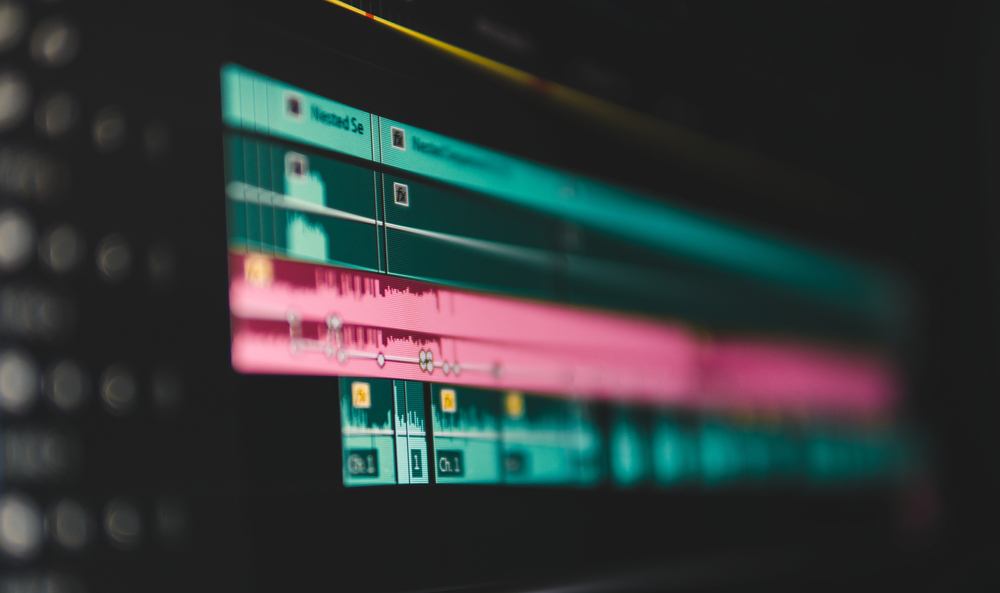
製造設備のスマート化、世界の「常識」と日本の「非常識」
IoT(Internet of Things)を活用した、製造現場のスマート化、いわゆる第4次産業革命(Industry4.0)が全世界的に進みつつあります。その一方で、日本の現状は下記のように、世界の潮流と大きく異なっています。
世界の現状 | 日本の現状 | |
①産業用PCの普及率 | 生産設備の制御でPCの導入が進む | PLCによる制御がまだ主流 |
②取組の主体 | 官民連携によるIndustry 4.0の導入が進む | 企業ごとの取組が多く、足並みがバラバラ |
③SIerの活用 | ライン設計からメンテナンスまでを独立SIerに任せる傾向が進む | 自社系列のSIerが設計・メンテナンスを行うことが大半 |
この記事では、こうした世界と日本の差異について、ご紹介をしていきます。
FAプロダクツでは、工場設備のメンテナンス・リプレースにご対応いたします。
- 老朽化した設備を入れ替えたい
- 手書き図面をデジタル化したい
- 緊急のメンテナンスをお願いしたい
といったお悩みのお持ちの方は、ぜひ下記フォームやお電話より、お気軽にお問い合わせください。弊社が納品したもの以外の設備にもご対応いたします。
こちらの記事は連載です。ほかの記事は、下記よりご覧ください。
連載【日本の製造業における産業用PC導入の現状と課題】 |
目次
1.PC制御が主流となりつつある世界、PLC制御が中心の日本
「平成30年版 情報通信白書」は、産業用途のIoTデバイスの数は、2020年までに世界で42.4億台から94.9億台までに増加すると予測しています。
一方、日本におけるIoT化はまだまだ進んでいません。
三菱UFJリサーチ&コンサルティング株式会社による「我が国ものづくり産業の課題と対応の方向性に関する調査」によると、製造工程のデータ収集を行っている会社の数は、2017年の67.6%を境に減少。2019年時点で51.6%にまで落ち込んでいます。
なぜ、こうした現象が起きているのでしょうか?
(1)ネックは「PLCを前提とした生産設備の普及」
日本の製造現場での主流は、PLCによる制御です。耐環境性を持つことから多くの製造現場に導入され、現場で長い間活用されてきました。
各メーカーによる機能拡張も進み、設備制御という面では非常に柔軟・かつ複雑な対応もできるようになっています。
いっぽう、メーカーごとに制御方法が細かく異なるため、一度ひとつのメーカーを入れてしまうと、他への切り替えが行いづらいという現状があります。
また多くの設計者はラダー図によるシーケンス設計を行っているため、プログラミング言語が必要となるPC制御に対応できる人材が少ない面も切り替えのネックとなっています。
(2)なぜ世界ではPC制御が主流となっているのか?
ではなぜ、PC制御が世界では主流となっているのでしょう?
その理由に、製造業において産業用PC導入を用いたデータの分析・活用が重要となっている点があげられます。
中でも特に重要となっているのが「エッジコンピューティング」と呼ばれる技術。
これはデータ端末の近くにサーバを設置し、端末から近い位置でデータ処理を行ってから上位サーバにデータを送信する技術です。
出典:総務省「平成の情報化に関する調査研究」
製造業においては、大量のデータを工場単位で処理してから基幹システムなどに統合することで、大量のデータを低遅延で扱うことができるようになります。
こうした処理を行うためには、制御だけでなく、データの収集・分析が可能な産業用PCが欠かせません。
上記の理由から、世界的には産業用PCの導入が増加しつつあるのです。
株式会社ミック経済研究所発行の「エッジコンピューティングで拡大する産業用PC市場の現状と展望2019年度版」によると、産業用PC市場のエッジコンピューティング用途の市場割合は、2018年が全体の5%程度のところ、2022年度には20%を超えると予測されています。
エッジコンピューティングだけでなく、AIを用いた検査工程の自動化などのDX実現には、PLCよりも幅広い用途に対応できる産業用PCが必要となるのです。
2.官民連携でスマート化を進める海外、制度や人材面に課題を抱える日本
また、官民の連携という面でも、日本と世界ではスタンスの違いがみられます。
比較・検討しつつ解説していきましょう。
(1)世界での取り組み事例
「平成29年度情報通信白書」より、世界の取り組み事例を見てみましょう。
このように、各国いずれも取り組みを行ってきていますが、世界的な潮流で見ると、官民連携を起点とした取り組みが中心となっています。
たとえば、製造業大国としていち早く改革に乗り出したドイツの「Industry4.0構想」は官民連携のプロジェクトです。
そのほか、米国では米国国立標準技術研究所(NIST)とIBM,Intelなどの企業が共同でIoTに関するコンソーシアムを立ち上げているほか、イギリスでは産学官連携の拠点である「Catapult Center」と呼ばれる施設を各地に設置し、中堅・中小企業をサポートしています。
(2)日本における課題
一方で日本では、官民が連携してイノベーションを行う施策は少なく、各企業が個別に製造業のスマート化、DX化を進めているのが現状。
そのためか、売上高が小さい中小企業ほど、取組への意欲が低いという傾向がみられます。
出典:平成29年度情報通信白書
※縦軸は「第四次産業革命に向けた取組をしている」と回答した企業の割合
さらに、日本および海外企業の持つ課題感を細かくみたものが下記の図です。
出典:平成29年度情報通信白書
※ITAC企業……IoT推進コンソ―シアムの会員企業。
上記から、日本企業は海外企業と比べて、
- 標準化やデータ流通に関する制度
- 対応できる人材や能力の不足
の二点に対し、より強い課題感を抱えていることがわかります。
特に制度面での課題感は、官民連携で行っている他国と比べ、顕著な差が見られます。
3.生産設備メンテナンスを外部に委託する世界・自社内で行う日本
前章で挙げた課題のうち「対応できる人材や能力の不足」という点について、より詳しくみていきましょう。
(1)自社内に保全部門を持つ企業は多いが、人材数は減少
公益社団法人日本プラントメンテナンス協会の「2019年度メンテナンス実態調査」によると、製造業で自社内に保全部門を設置している企業は全体の85.4%にのぼります。
一方で従業員数の推移をみていくと、2018年度から保全部門の人員が大幅に減少。
製造部門の人員数との比率も、前年度の19.6%から12.8%に急減しています。
拡大している製造部門と比較して、人員数が追い付いていない現状がうかがえます。
(2)世代交代が一気に進み、技術の継承が課題に
いっぽうで年齢比の推移をみていくと、2018年度から20代以下の人材が急増し、世代交代が急速に進みつつあることがわかります。
それに伴い、保全部門のスキル保持者の年齢構成比は高齢化が顕著に。
日本の製造業は、各企業ごとに独自の判断基準を定めていることもあいまって、保全に関わる技術が属人化しているという現状があります。
こうした現状と、人員数のさらなる減少を考えたとき、製造業においては
- 効率的なメンテナンス体制の確立
- ロボット・AIなどの新技術に対応できる人員の確保・育成
がいっそうの課題となると考えられるでしょう。
いっぽうで海外では、専門的なスキルを持つロボットSIerに外注を依頼し、コスト管理を行うという方針が主流となっています。
人員の育成や社内体制の整備には時間とコストが必要となるため、常時対応が可能な外注業者と契約したほうがトータルでのコストが下がるためです。
スキルを持つ人材の高齢化・減少にともない、日本においても今後、同様の流れが進むと考えられるでしょう。
4.おわりに
スマートファクトリー化における日本と世界のスタンスの違い、およびその原因と課題についてご紹介してきました。
製造業が海外との競争力を維持するためには、「生産量可変・生産変更がスピーディ・多様な製品種に対応可能」な工場へのシフトが重要となってきます。
そのために、製造現場への産業用PCの導入が欠かせないのです。
次回は、世界で産業用PCの導入が進んでいる現状とその原因についてまとめていきたいと思います。
連載【日本の製造業における産業用PC導入の現状と課題】 第二話:世界で産業用PCが導入される理由は?スマートファクトリーとの関係を解説 第三話:日本に産業用PCが導入されない理由は?3つの視点から解説 第四話:産業用PCが実現するDX!製造設備のスマート化でのメリットを紹介 |
関東最大級のロボットシステムインテグレーター 生産設備の設計から製造ならお任せください
050-1743-0310 営業時間:平日9:00-18:00