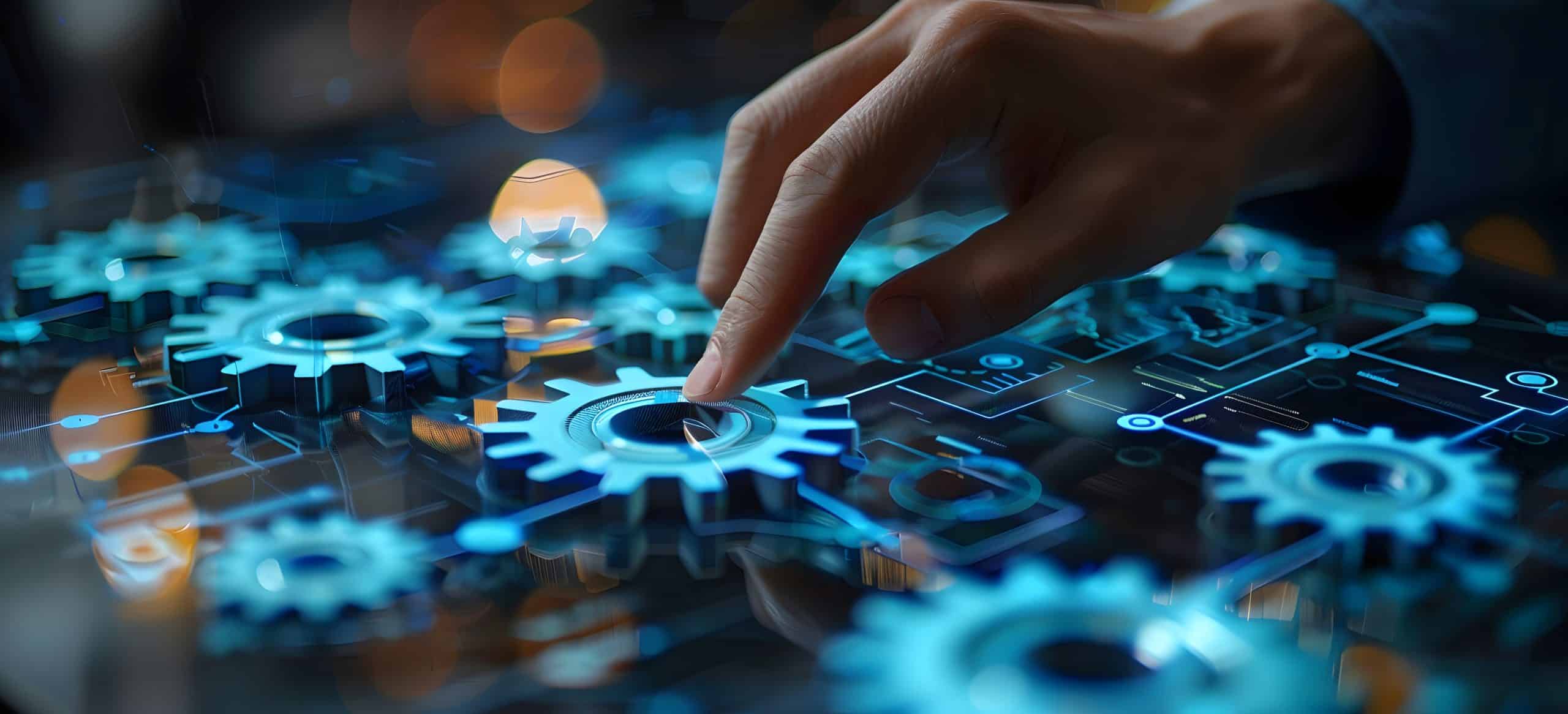
製造業における業務プロセスとは?最適化の方法やメリット、IoT化
製造業の現場では、日々の業務の中で需要の急変、納期遅れ、品質ロスなどの様々なトラブルが発生しています。また、製造コスト増、在庫増加、人手不足などの経営課題に頭を悩ませている方も多いのではないでしょうか。
このような課題に対しては、個別課題の分析を踏まえ、部門間にまたがる業務プロセス全体の最適化を目指す考え方で取り組むのが効果的です。
なぜなら、製造業は営業、資材、開発、生産、設備といった、多部門の分業で構成されているからです。
もし各部門が全体を考慮せずに個別に最適化をはかったら、業務プロセス全体では生産性が落ちてしまうかもしれません。
この記事では、製造業における業務プロセスとは何か、その改善の手法、気を付けるべきポイントについて解説していきます。
もし、コンサルティングを受けて、
・省力化、省人化してコストダウンしたい
・生産性アップして売上を上げたい
・人的ミスを減らして品質価値を高めたい
・どのメーカーの自動化設備を使えば効率的かわからない
という場合は、お気軽に株式会社FAプロダクツまでお問い合わせください。
関東最大級のロボットSIerとして、最適化のご提案をさせていただきます。
目次
1.製造業における業務プロセスとは何か?
(1)業務プロセスが意味するもの
まず、業務プロセスとは何を指すかについて説明しましょう。
業務プロセスとは、企業がその事業目的を達成するために日々行う様々な業務の流れを指します。
製造業であれば、その典型例はマーケティング→新製品開発→宣伝→受注→部品調達→製造→出荷→販売→アフターサービスという一連の流れです。
このように、営業・製品開発・資材・生産・物流といった様々な部門が連携しながら進む業務プロセスこそが、製造業にとっての企業活動そのものであることがわかります。
さらに、重要な経営資源である「人」を司る総務・人事、「金」を司る財務・経理といったバックオフィス部門の活動も忘れてはいけません。
業務プロセスとは、企業が存続・活動するため、部門間で連携しながら行われる日常の業務と、それによる利潤獲得までの流れを意味しています。
(2)業務プロセスと業務フローの違い
業務プロセスに似た用語として、「業務フロー」という言葉もよく使われています。
混同しがちなこの二つの言葉にはどのような違いがあるのでしょうか。
業務プロセスとは、事業全体を構成する一つ一つの業務が何のためにあるか、どのように連携しているかを指す言葉です。
一方、業務フローは、業務プロセスを構成する個別の業務の中で、具体的なタスクの流れやトリガーとなる前工程からの流れ、作業手順を視覚的に示したものです。
つまり、業務プロセスが各業務における「目的と行動内容」を定義するのに対し、業務フローは、各々の業務プロセスを「実行するタイミングと手順」を定義しています。
企業活動全体から考えれば、一連の業務プロセスの構成要素として、各業務に「業務フロー」があると考えればイメージしやすいでしょう。
製造業における業務プロセスについては以下の動画も参考になります。
引用:製造業のデータ分析 第17回 業務プロセスの図解化(全25回)
引用:フローチャートが描けない理由【業務改善】【プロセス可視化】【業務フロー】#136
引用:PDCAサイクルとは【改善活動の基礎 カイゼンの基本編:第7章】
2.業務プロセスの最適化のメリット
次に、製造業において業務プロセスの最適化によって得られるメリットがどのようなものか考えてみましょう。
大きく分けて、「事業によって生み出される付加価値の向上」と、「企業そのものの経営基盤の強化」という側面が挙げられます。
(1)付加価値の向上
まず、業務プロセスの最適化によって期待できる付加価値の向上について説明します。
例えば営業部門が受注見込み情報の正確性を高め、顧客の需要変動をよりタイムリーに生産計画へ反映する仕組みを構築するとします。並行して、生産部門・資材部門が最新情報に基づき、最適な生産計画や部材調達を行う体制を整えていれば、どういった効果が期待できるでしょうか。
一つ目は、生産性の向上です。
生産部門・資材部門が、営業部門の発信する最新情報に基づき、最適な生産計画や部材調達を行えれば、結果として生産性は高まるでしょう。逆に売れ筋ではない製品の製造を減らす調整ができれば、無駄な在庫、資材を減らし、利益率のアップにもつながります。
二つ目は、販売機会と顧客満足の向上です。
タイムリーな生産調整によって、顧客が欲しいタイミングを逃さず販売できれば、売上げと顧客満足度がアップし、次回以降の受注増という好循環も期待できます。つまり、この場合は営業部門、生産部門、資材部門の三者全てが業務プロセスの中でうまく連携できるかどうかで、生み出せる付加価値が変わってくると言えます。
(2)経営基盤の強化
業務プロセス改善によってもたらされるもう一つのメリットは、経営基盤の強化です。
製造業に限らず、企業の4大経営資源は人・モノ・カネ・情報と言われています。この4大経営資源をいかに無駄なく有効活用できるかによって、業績だけでなく、長期的に成長するか衰退するかが左右されるのは間違いありません。
例えば、製造工程の中に、高い技術を持った一部の熟練工にしか操作できない機械があったとしましょう。このような状態は業務の属人化と呼ばれ、高いリスクをはらんでいます。
生産高が熟練工という特定の人材に依存しているため、もし熟練工が退職したり、他社へ引き抜かれたりしたら、たちまち生産に支障を来しかねません。
この場合も、業務プロセス改善により対処する必要があります。
具体的には、人材育成によってこの装置を扱える熟練工を増やす、またはロボットなどの設備投資によって工程そのものを自動化するなどの方法が挙げられるでしょう。
他の4大経営資源である、モノ、金、情報についても、このようなリスクがあるかどうかを常にチェックし、業務プロセス改善の中で先手を打った対策を行うことが重要です。
3.業務プロセス最適化の4ステップ
では次に、業務プロセスの最適化をどのようなステップで進めるべきか、順を追って説明していきます。
市場や経営環境の変化が激しい今日では、今日の正解が明日も通用するとは限りません。業務プロセスについても同様です。
一度の改善で満足するのではなく、より良い姿を目指して絶えず見直しを図る姿勢が重要だと言えます。
(1)業務プロセスの見える化
一つ目のステップは、業務の全体を構成する一つ一つの要素を把握することです。これを業務プロセスの「見える化」と呼びます。
具体的には、業務の流れをできるだけ細かく切り分け、その一つ一つの要素が何をトリガーに行われているか、また、前後の業務との繋がりと役割をまとめていく作業となります。
この作業では、業務全体の流れを視覚的に理解できるように、フローチャート図を用いて、業務の内容と前後とのつながりが一目で分かるようにまとめると良いでしょう。
また、生産情報をデータ化するという方法も、見える化の手段として有効です。客観的なデータを用いれば、課題がどこにあるのかの把握が容易になるためです。
業務プロセスの「見える化」が完了したら、次の段階は課題の分析となります。
(2)課題の分析
業務プロセスの見える化を踏まえて、次は具体的な課題の分析を進めます。
例えば、ある工程において本来の装置能力の50%しか稼働できていない、というデータがあったらどうでしょうか。
ここから、問題点の奥にある真の課題を見つける必要があります。
そのための手法として、トヨタ生産方式により考案され、製造業にて広く活用されている、「なぜなぜ分析」という方法を紹介します。
これは、ある問題に対し、「なぜ」を5回繰り返すことによって根本的な理由を探る手法です。
課題は、「ある装置Aの稼働率が20%落ちた」です。
①なぜ稼働率が落ちたのか? →装置Aの待機時間が長いため
②なぜ待機時間が長い? →前工程の不良率が上昇したから
③なぜ前工程の不良率が上がった? →作業者のミスが30%増えた
④なぜ前工程で作業者のミスが30%増えた? →作業者が新人に変わったから
⑤なぜ新人のミスが多い? →マニュアルが分かりづらいから
なぜ① | なぜ② | なぜ③ | なぜ④ | なぜ⑤ |
装置Aの稼働率が落ちた理由は? | 待機時間が長い理由は? | 前工程の不良率が上がった理由は? | 前工程の作業者のミスが30%増えた理由は? | 新人のミスが多い理由は? |
待機時間が長いため | 前工程の不良率が上昇したから | 作業者のミスが30%増えた | 作業者が新人に変わったから | マニュアルが分かりづらいから |
5回のなぜを繰り返すことにより、隠れていた本当の課題が見えてきました。
このように、業務プロセスの見える化と課題の把握ができたら、次にすべきことは、課題の重みづけと優先順位を決めるという段階です。
(3)改善施策の実施
課題の分析が終わり、いよいよ具体的な改善の段階まで来ました。
この事例の場合、どのような方法があるでしょうか?
一見、前工程の作業者を新人からベテランへ交代させればミスが減って問題が解決するかもしれません。
しかし、この方法だけでは、この業務が「属人化」している状況を固定することになるので、適切な解決策とは言えません。
今後、この作業者が再び人事異動で替わったら、再び同じ問題が起きる可能性があります。
では、どういう方法を取るべきなのでしょうか?
・新人でもミスしないように前工程のマニュアルを改善する
・前工程を自動化して、人が不要な作業とする
・前工程を外注する
このように様々な業務プロセスの変更が考えられますが、費用と効果、実施までにかかるスピードなどを考慮して対策を決める必要があるでしょう。
また、この対策立案時に重要なのが、達成目標(KPI)の設定です。
達成目標(KPI)とは、Key Performance Indicator(キー パフォーマンス インジケーター)の略で、「重要業績評価指標」と訳します。これは、最終目標の達成に向けたプロセスを適切に実行できているかどうかを定量的に評価するために設ける指標のことです。
今回のケースでは、前工程で発生する不良率についての指標を設けることで、最終的に装置Aの稼働率を改善することに繋がります。
【参考記事】
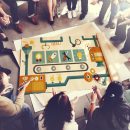
(4)改善後の運用と見直し (PDCAサイクル)
このような流れで業務プロセス改善について説明してきましたが、改善後の定期的なケアも重要です。なぜなら、一度の改善で完璧な結果を得ることは難しいからです。
改善結果を評価しさらなる改善のために行う手法としては、PDCAサイクルが代表的です。PDCAサイクルとは、PLAN、DO、CHECK、ACTIONを略したもので、以下のような流れで回していきます。
①Plan(計画)-改善目標の設定と計画立案、KPI の設定
②Do(実行)-計画を実行する
③Check(確認)-定期的に実施状況を確認、見える化により状況を把握、なぜなぜ分析
④Action(改善)- 最新の課題に合わせて計画を見直し、KPIの修正などを検討
ある改善を進めていく中で、別の課題に直面することもあるため、定期的に業務プロセスを様々な角度からチェックし、改善を継続するという姿勢で取り組むことが重要です。
【参考記事】
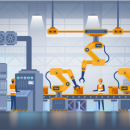
4. 工場のIoT化による業務プロセスへの貢献
モノがインターネットに直接つながるIoTという概念が製造業の分野でも近年導入が進み、業務プロセスの効率化のために活躍しています。いくつか事例を紹介していきます。
(1)見える化への貢献
一つ目の活用事例は生産ラインの見える化への貢献です。
例えば、生産ライン上の各装置や監視カメラなどの機材が直接インターネットで繋がることにより、従来の目視などよりもはるかに大量のデータを入手できるようになりました。
具体的な効果としては、生産工程の稼働状況をリアルタイムで見える化したり、ライン上の異常や故障の早期発見、品質検査の精度向上としての活用も期待できます。
(2)離れた拠点間での連携
IoT化は離れた場所でも瞬時にデータを共有できるので、特に離れた拠点間で業務プロセスを共有する際の支援ツールとしてメリットが大きいです。
工場のIoT化により、拠点をまたがった業務プロセスの見える化や部門間の連携が向上すれば、コストダウンや品質の安定化に大きく貢献するツールとなるでしょう。
(3)人材育成への活用
IoT化の推進は、昨今深刻化している人手不足や、世代間の技術伝承のためのキーとして重要な役割を果たしています。
具体的には、従来、長い年数をかけて培われてきた熟練者のスキルが、IoTによって勘や経験ではなくデータとして残せることになります。
このデータを活用し、マニュアルに落とし込めば次世代の人材育成にも活用できるのです。
【参考記事】
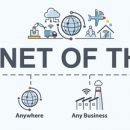
5.業務プロセスに関するご相談は株式会社FAプロダクツへ
FAプロダクツは年間200台もの実績がある関東最大級のロボットシステムインテグレーターです。一貫生産体制をとっており、設計から製造までをワンストップで対応。費用・時間にムダなく最適化を行うことができます。
業務プロセスについても、ぜひご相談ください。
お打ち合わせから原則1週間以内に「お見積りとポンチ絵」をご送付いたします。
【ポンチ絵とお見積りのサンプル】
テキストやお電話だけでは伝わりづらいゴールイメージを共有し、スピード感を持った対応を心がけています。
また、同社の「画処ラボ」では、画像処理を用いた外観検査装置の導入に特化し、ご相談を受け付けています。従来は目視での官能検査に頼らざるを得なかった工程の自動化をご検討の際などにご活用ください。
業界最大級の画像処理検証施設を開設!
「画処ラボ」ではルールベースやAIの画像処理を専門エンジニアが検証。ご相談から装置制作まで一貫対応します。
所在地・連絡先等 | 営業品目 | 実績 |
茨城県土浦市卸町2丁目13-3 TEL.050-1743-0310(代表) FAX.050-3156-2692(代表) https://jss1.jp/ |
・産業用ロボット ・生産設備合理化・省力化の設計及び製作 ・基板電気チェッカーや貼合・折曲など ・治具の設計・製作 |
NM社(電子部品の製造販売)、HS製作所(情報通信・社会産業・電子装置・建設機械・高機能材料・生活の各システム製造販売)、TT社(ショッピングセンターなどリテール事業)、SM社(自動制御機器の製造・販売)、OR社(自動車安全システムの製造販売) |